SUPPORT SERVICES- INSTALLATION
Pipe work, electrics, pneumatics, testing, flushing.
Electrical
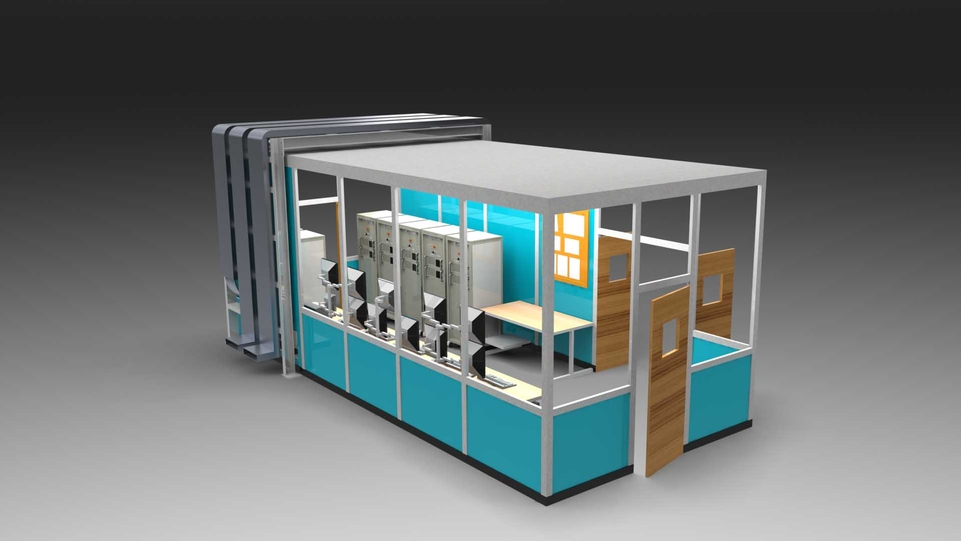
Our team of highly knowledgeable and experienced engineers have worked extensively in design, specification, procurement, installation, commissioning and operations and maintenance of electrical power systems. Our success is built on working with the best people and using our key skills to design and implement electrical power systems to meet the needs of our clients’ requirements today and into the future.
We have over 20 years of experience on joint projects with RTC Ltd who provide us with Software design, Data Acquisition, Control Systems, Servo control and starter panels for hydraulic power units.
All aspects of system control are handled, from high-level man-machine interface and machine sequencing to low-level time critical closed loop PID ( Proportional, Integral and Derivative ) control, feed-forward terms for loop optimisation and spike suppression
Our test rig control systems consist of a “top end” graphical user interface, running in an industrial PC, which controls and commands the operation of one or more “embedded” controllers. These are also industrial PC’s, without screens or keyboards, which run high speed real-time software to perform such tasks as PID control, rig motion control, sequencing and timing, load profiling, alarm monitoring and safety shutdown
Profiles are edited and stored on the user interface PC and downloaded to the embedded controller prior to running the test rig. The servo control system is digital, so we are able to vary the PID terms of the controller to cope with extreme cases of static and dynamic operation. Customised algorithms are developed and optimised in the servo controller to eliminate the effect of any non-linearities found in the rig or unit under test.
Our servo control systems interface to the standard range of instrumentation equipment ranging from load cells, torque transducers, pressure transducers, flow meters, tachometers, temperature transducers, rotary and linear position transducers including LVDTs, RVDTs, VRVTs and encoders
RTC has a strong multi-disciplinary team of software engineers, experienced in all aspects of engineering system design. They have extensive experience in ‘C’, National Instruments LabView, Mathworks’ Matlab/Simulink, Dymola and assembler low level programming.
The graphical user interface is authored using National Instruments’ LabWindows/CVI. The development of this interface over the years has been driven significantly by customer feedback, so is very much tuned to the particular requirements of the industry and offers many features to reduce the operation of even the most complex rigs to simple, intuitive and easily documented operator procedures.
Each bespoke control system is unique, the capabilities of our controllers have advanced and continue to advance with available technology. In spite of this, there is a conscious effort to maintain a common “look and feel” to the user interface, so that any requirement for operator re-training on a new rig tends to be limited to issues regarding the new unit under test.
Control software is written using Matlab/Simulink and implemented on an industrial PC. Using such a platform, running as an “xPC embedded target system”, we currently embed up to four independent control systems, each supporting full non-linear PID control at 1kHz, into a single PC. Concurrent with the PID control, each controller may generate real-time load command profiles, check multiple inputs for alarm limit violations, perform I/O sequencing and supply continuous status information to the user interface via an Ethernet link. Apart from initial set up, the embedded PC requires no intervention from the user interface to perform these tasks. Even with such an apparently heavy workload, the processor still spends up to 70% of its time in idle, so there is plenty of spare capacity for the addition of customised features if required.
The liaison of Comar with RTC Electronics is a proven success story, combining the skill set of each company to achieve a solution to even the most complex requirements .
Hydraulic
Comar has always believed it must fully support whatever it sells. Therefore, we offer a wide selection of hydraulic installation practices to suit most customer requirements. Design engineers at Comar are constantly working on improving existing systems while creating new installations to meet the needs of our customers.
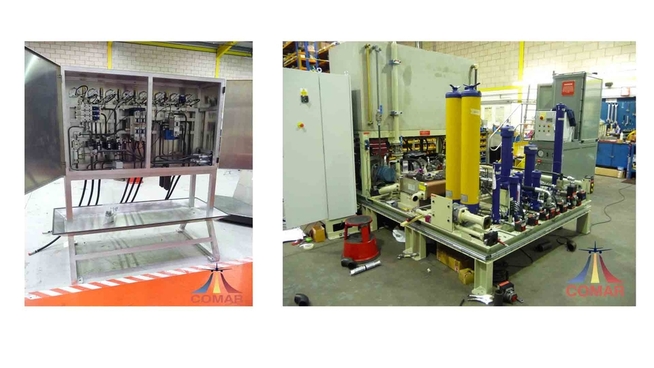
For over 35 years, Comar has worked with the leading manufacturers of hydraulic equipment to develop hydraulic systems that comply with customer standards.
Comar engineers have worked with its suppliers to design and develop systems that have the durability to withstand the abuse of the end user.
Every Comar hydraulic installation comes standard with detailed installation instructions and all components required to operate.
Installation and design experience, combined with unmatched support, ensure the Comar hydraulic installation provides safe operation and optimum performance for your Test rig.
Pneumatics
As a function of our test equipment supply, pneumatics is very often used for low force applications and for pressure testing of components, air under water rigs have been supplied measuring the pressure drop over a period of time.
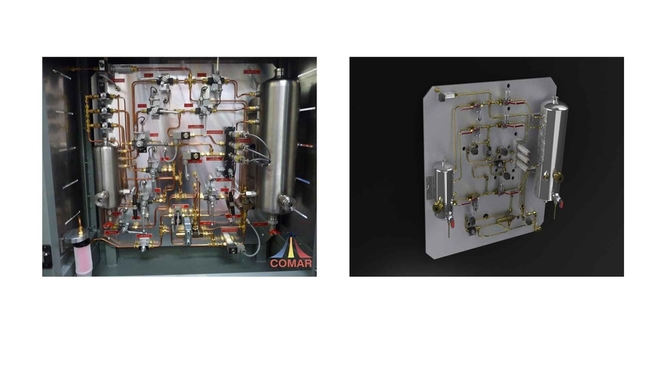
Pneumatic Panels
We have the capability to build a variety of custom pneumatic control systems and panels. We can build to your current design or assist you with a new design. With our extensive product knowledge we can integrate electrical and pneumatic technologies to create the perfect custom solution for your application.
Electro-Pneumatic Control Systems
With our extensive product knowledge we can integrate electrical and pneumatic technologies to create the perfect custom solution for your application. We can build to your current bill of materials or we can help value-engineer your current system by substituting components from product lines we represent. Our engineering staff is ready to assist you with your next design.
Mechanical
What is Mechanical Assembly?
Mechanical assembly is the process of assembling individual components together to become a working module. Assemblies can consist of various parts, from machined parts to commercial standard parts such as screws, nuts, and pins. It may also include plastic, metal, or a variety of other materials. The processes of combining the components may include mechanical torque, brazing, welding, or a variety of other possible processes.
At Comar we possess the skills associated with assembly best practices, our skilled team build simple assemblies through to complex mechanical, hydraulic and electromechanical projects. The company operates a dedicated assembly areas that can be honed to meet specific customer requirements and includes complete testing facilities.
I would like to invite you all for a curry to show my appreciation of the excellent effort during the C-series Safety of Flight testing, thank you for the tremendous achievement over the last few months.